If you have an asphalt shingle roof, having the shingles blow off in the wind is one of the ways it can fail. This post explores what this failure looks like, the possible consequences, some of the causes, and how to ensure this doesn’t happen to you.
Shingle blow-off happens with both new and old roofs. The more common failures happen near the rakes/gables and below the ridge-line. There are several causes, some relating to the quality of the installation, and some to the quality of the product.

New roof, shingle blow-off
(Click on image to see it full size)
This image shows a recently installed roof (about 2 years old), which already experienced shingle-blow-off. While the shingles themselves were installed with a certain degree of care in terms of placement, the nailing pattern shows that the installer did not follow the standard practice, and nailed them too high, which shows either that they didn’t care, or were in a hurry and did place the nails in the right places. In addition, this particular roof is getting winds directly from the lake without any protection, and the roofers did not attempt to increase the wind resistance of the roof by using any of the techniques for high-wind installation.

New roof with shingle blow-off
(Click on image to see it full size)
This is a new roof, installed in the fall. In the spring, the roof is already showing wind damage. It appears that the fall installation resulted in the tar strips not sealing, and although the roof “looks” well installed, it will continue to fail. To quote the warranty from one shingle manufacturer (BP) ( http://bpcan.com/CMS/Media/32629_53_en-CA_0_WARRANTY_Shingles_Ltd_EAST.pdf ):
“For the Warranty against wind blow-off to take effect, the self-seal adhesive must be subjected to sufficient heat to activate the bond. When the shingles are installed in environmental conditions that will not produce such temperature or in very windy areas, the shingles should be sealed down with spots of asphalt plastic cement as specified in CSA A123.51-M85. In addition, contamination of the self-sealing adhesive by dust or foreign matter may prevent the sealing strip from achieving a full thermal seal. Prior to sealing, shingles are more vulnerable to wind damage.”
The concern about proper sealing of the tar strip is also seen in the warranty language of IKO (another shingle manufacturer): (http://www.iko.com/publication/iko-manufacturing-warranty/wppa_open/):
(i) the Limited Wind Resistance Warranty will only apply if: (a) the Shingles were installed using roofing nails (not staples) in strict accordance with the instructions on the wrapper and (b) for installations in Canada during the fall, winter or in cool weather, the Shingles have been manually sealed at the time of installation, and for installations at all other times in Canada, and at all times in the U.S., the Shingles have been manually sealed at the time of installation, or have had the opportunity to seal down;
In short, if the installation of the shingles takes place late in the season, then the roofer needs to take extra precautions to ensure that the shingles do NOT lift prior to the roof having enough heat to melt the tar strips, and therefore effect the seal.
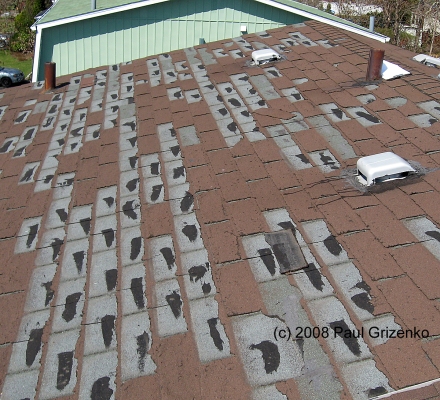
Shingle blow-off despite attempt at “sealing”
(Click on image to see it full size)
In the above example, the roofer obviously considered the possibility of blow-off and dabbed each shingle with some roofing cement. However, they did not follow the recommended practice, and the roof still ended up with shingle loss.

Workmanship as a contributing factor to shingle blow-off
(Click on image to see it full size)
This example shows the effect of poor workmanship. The nailing pattern is too high, the shingle alignment is poor, the flashing work is certainly lacking, and there any many signs of a hurried installation. It can be seen that some repairs were attempted.

Shingle blow-off due to loss of shingle flexibility.
(Click on image to see it full size)
As the asphalt shingles age, they become more brittle. In some products, there is also shrinkage of the felt and some clawing or curling. In the above case, the shingles did, for the most part, stay flat, but as can be seen on a number of shingles, started to crack horizontally. If the tar strip is only partly sealed, then this provides very little resistance to wind forces, with the result that the shingles are susceptible to blow off.

Shingle blow-off can lead to deck damage.
(Click on image to see it full size)
In the above example, we can see that the wind blow-off exposed the deck. This is another example of the roofer apparently cutting corners by not installing any kind of underlayment under the shingles. If the wind was strong enough to break off the shingles, it is also strong enough to blow rainwater in between the shingles and onto the roofing deck. If the roofing deck is not protected by underlayment, then this will result in persistent wetting of the deck. Depending on the type of decking, this persistent wetting may cause delamination of the plywood, or complete loss of structural integrity in OSB, or contribute to rotting of wood.

Deck damage due to lack of working underlayment.
(Click on image to see it full size)
This image from inside an attic, shows what happens when there is no underlayment (or poorly installed underlayment). Water has been seeping into the deck, causing:
- Delamination of the plywood (as can be seen by the cracking of the wood veneer),
- Rusting of nails (every nail is rusty)
- Entry of water into the attic interior, which increased humidity in the attic and supports growth of mold (see the dark marks on both the underside of the wood, and in the insulation,
- Loss of decking integrity (as can be seen at the movement of the wood at the H-clips).

Deck damage due to missing underlayment.
(Click on image to see it full size)
In the above case, the plywood decking lost enough integrity to require complete redecking. Fortunately, the mold inside the attic was minimal (due to decent ventilation that ended up drying the moisture as it seeped in), so additional measures of removing the insulation were NOT needed. The cause of the problem was the failure of the roofer to install appropriate underlayment, and to take into account the slope of the roof and the way the roof system worked.
How do you avoid this kind of damage?
There are two solutions:
- Choose installers who take the time to do it right, who are aware of the weaknesses of each type of material they work with, and who provide the proper second (and third) line(s) of defense in anticipation of strong weather events.
- Choose products and installation methods that have a proven track record of preventing the kinds of damage seen in these photos.
Elsewhere on this blog (in the articles section), I’ve posted an article on how to get a good quote for your roof. What is relevant to this section is the degree of care the prospective roofer pays to understanding your actual situation, and to ensure that the resulting quotation addresses all of the needs. It should be clear that in most of the above cases, work was done in a hurried manner, without consideration of how failure could occur, and without providing for adequate countermeasures to these modes of failure.
The most effective way to avoid having to worry about blow-off, is to use products and installation methods that CAN withstand wind damage, and associated issues such as damage by wind-driven rain. These products and installation techniques are more expensive than what one would pay for conventional asphalt shingles, but they look expensive only when ignoring the true durability and the true cost of repairing damage caused by poor choices.
If you are tired of worrying whether your roof will protect your home from the next wind storm, give me a call to explore the options that you need to consider.
(c) 2014 Paul Grizenko
Update (January, 2017): This article has had thousands of views. If you have some specific questions on any aspect of the discussion above, please use the comment form (next to the post title) to post the question or comment. All comments are moderated, and will appear after review and approval.